Concrete pumping hoses play a vital role in ensuring a smooth flow of concrete on the job site. They have to be able to handle the pressure and the concrete must be pumped quickly. The line will clog up and workers will need to scramble in order to get it moving.
It is important that contractors follow the safety guidelines of the ACPA to avoid this. They should also inspect the hoses for wear and leaks.
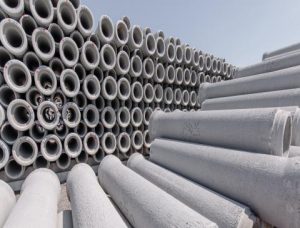
how to choose concrete hoses
A concrete pump hose is an important part of a concrete placement system. It carries the concrete from the truck to the pumping mechanism. It must be long enough to reach the pouring site, but not too long that it gets damaged. In addition, it should be able to resist high pressures and abrasion.
The most common type is the steel-wire reinforced concrete pump hose. It is made up of an inner rubber layer with a reinforcing sheet and a steel-wire winding. This type is suitable for high-rise buildings, roads and tunnels. It can also be used for large water conservation projects and nuclear power stations.
The right hose is essential for safety and performance. For example, a concrete hose that is too short can cause the concrete to spill out of the tank. It can also cause a loss in efficiency and poor performance.
When using a boom pump, it is important to ensure that the outriggers are fully extended and the ground is stable. This will help to reduce the risk of tipping over and prevent injuries for workers. It is also important to stay clear of overhead power lines and keep workers away from hose ends. A good quality hose should have a working pressure of 1275 psi and be made from durable materials.
concrete hose connector
Concrete hose connector is used to connect the concrete pumping hose to the end of the concrete pump. It is a heavy-duty hose that is designed for pumping concrete, fireproofing, plaster, shotcrete, and grout materials. This abrasion-resistant concrete placement hose features full-flow internally expanded couplings that prevent material build up and allow for higher working pressure ratings.
The hose connector consists of a hardened shank and a flexible seal within the coupling that mate with each other. The hardened shank has a U-shaped cross-section with edges that fit into the grooves in the coupling end. The flexible seal and a latch unit in the coupler make up a rigid interconnection between the two elements to ensure continuous flow of concrete. The operator releases the latch unit to release the couplings when it is time to replace or remove the hose, or wear tube.
Concrete has poured out of the hose connector in a number incidents. This can cause a serious injury if it hits someone. These incidents have happened in high-rise buildings. The failure was caused by a cracked or failed part of the swaged end fitting. It is important to use a high quality hose connector with a stringent process for attaching it to the hose.
production standards for concrete hoses
An accident called "hose Whip" can occur when a hose is not properly fitted. When the concrete in the line is released, it builds up pressure and forces the flexible hose end into the boom or ground. This can cause the hose to whip violently, hitting workers nearby. This is a serious safety issue that can have serious consequences. ACPA recently published a safety bulletin on this problem.
Regular inspections of the hose are necessary to ensure its safety. It should be checked for signs of damage and the hose and fittings should also be tested for hydraulic pressure and the thickness of the steel pipe. The business attaching the fitting end should maintain documentation on the hose examination and make it available upon request.
Attaching the hose to the concrete pump can be done either by crimping or swaging. The crimped fittings are easily visible due to their indentations (see photo 5). Some hose manufacturers will only certify their hoses for certain pressures if they are attached with the correct type of hose ends. These must be manufactured to the correct tolerances, and a strict assembly process must be followed. The hose should be properly cleaned to reduce the likelihood of a blockage. It is important to clean the area around the hose, and only use concrete mix that can be pumped.