The production process of steam hoses includes a number of steps. This includes evaluating the temperature ranges, chemical compatibility and pressure requirements. They should be resistant to heat, steam and not react with material being transported.
Another important practice is thoroughly draining a steam hose after every use. This prevents a type damage called popcorning. It is caused by the absorption of water vapor into the hose tube walls. The moisture is absorbed, then cooled and condensed into water. This water remains trapped within the hose.
Steam hoses: advantages and disadvantages
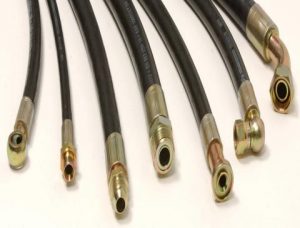
Steam hoses can be used to transfer hot water under pressure in a variety of applications. These include steam cleaning, steam pumping, heat control, flame prevention, thawing and blowout service. These hoses are suitable for harsh environments, such as shipyards and chemical plants. However, they must be properly specified and handled to avoid dangerous accidents.
When a steam hose is not in use, it should be drained completely and stored in normal temperatures to prevent damage. It should not hang on a hook or nail, as this can puncture the hose. This could lead to expensive leaks. The hose must be placed on a rack designed specifically for it. It should not be bent or kinked in any way. Avoid metal hangers as they can cause rust.
The inner rubber surface can deteriorate if the hose is exposed suddenly to a temperature change. This is called popcorning and can have a negative impact on the safety of the rubber hose. The hose should always be blown completely dry after each use to reduce the risk of it popcorning. The hose must also be checked regularly for gouges and kinks as well as loose couplings and corroded parts.
method for extending the service life of steam hoses
Steam hoses can be used in factories and processing facilities to channel steam that is dry, saturated or overheated. These hoses are typically designed to withstand temperatures up to 164degC. They are also designed to handle saturated steam pressures up to 100psi and minimal heat loss.
Many hoses have a maximum pressure of 250psi. This is only for safety reasons and they should not be used above that. If a hose is over-inflated, it will be damaged or rupture and can cause serious safety issues for workers.
There are a number of ways to extend the life of steam hoses. Proper storage and handling can help combat the effects of temperature changes, chemical vapors and sunlight, as well as other environmental factors, which can reduce hose life. Hoses with galvanized inlays are also resistant to rust, and last longer than other types of hoses.
The right hose is crucial for the operation of a refinery or processing plant. During regular inspections, it is important to observe and record conditions that place additional strain on the hose. This will help prevent premature rework or replacement, which can increase productivity and decrease cost. It is also important to develop a plan for routine inspections and replacements. This will help ensure that the hoses are in good condition, free of pinprick ooze, startup leakage at interlock fittings and tube popcorning failures.
Steam hose with a steel wire layer defect
Steam hoses are a vital part of industrial processes. To ensure safe operation and to extend their service life, they must be properly maintained. This includes ensuring that the hoses are correctly installed and that the fittings are in good condition. They also need to be de-pressurized after use to prevent the popcorning effect.
When steam reaches the steel inserts in rubber hoses, corrosion of the steel wire layer can occur. Inlays are usually made of galvanised steel. However, corrosion can cause the hoses to fail and let hot steam escape without warning. This is particularly dangerous in environments where steam can reach high temperature.
Twisting the hose is another common problem. This can significantly reduce the hose's lifespan. A hose's lifespan can be reduced by 90% with a twist of just 7%. Swagelok's hoses are not made with coiled reinforcement, as this type of construction is not suitable for pressures and temperatures of steam applications.
The best way to prevent these problems is to inspect the hoses regularly. Check the hoses for any gouges, cuts or blisters. The hoses should also be tested for leakage. When working near a hose of steam, workers should always wear protective gear. They should also install safety cables approved by OSHA at every junction in order to prevent the hose whipping around in the event that the couplings fail.