Blast hoses play a vital role in any blast system. They convey the abrasive media from the blast gun to the surface being blasted. Proper hose selection will improve production, lower maintenance costs and protect your blasters from electric shock.
Heavy duty abrasion resistant sand and shot blast hose that will accept higher working pressures and the most severe applications. Tube: smooth, antistatic, black, abrasion-resistant NR/BR rubber. Cover: black, antistatic, weather and abrasion resistant SBR/NBR rubber compound with cloth impression.
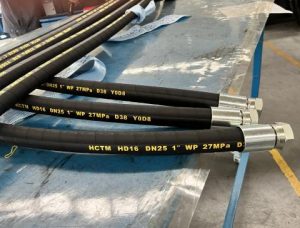
How to choose wear-resistant sandblasting Hose
The blast hose transfers the blast media to the nozzle (steel shot or sand). It is therefore important to choose a high-quality blast hose. Blast hoses will be exposed to high air velocity and pressure, so they must be able to resist abrasion. A good blast hose should have an internal diameter that is 3-4 times higher than the throughput holes on the nozzle.
The inner rubber of the blast hose must be natural or polyurethane and have a high concentration. It should have good wear resistance and bending resistance. The skeleton layer of a blast hose should be made from dipped tire radial wire. This type of wire is high-pressure bearing and has a good look.
A blast hose should be designed to meet the temperature and climate conditions of the worksite. This is because extreme temperatures can cause the hose to degrade quickly, resulting in loss of pressure and abrasion. It is also important to choose a blast hose that can be compatible with other parts of the blasting system, such as the blast gun and air compressor.
Kingdaflex offers two-ply or four-ply abrasion-resistant blast hoses for any application. These hoses can be paired with standard couplings, nozzle holders and blasting machines to increase efficiency on the jobsite.
Abrasion-resistant blasting hose couplings
Blast hoses transfer air and abrasive mixture from the blast machine to the nozzle. They have a thicker inner tube which resists abrasion. They are also resistant to ozone and weathering. They have a fabric reinforcement and an antistatic rubber cover. They are available in various sizes, lengths and bending radius. Abrasion resistant hoses are compatible with all types of abrasive blast media.
The couplings are one of the most important features in abrasion resistant sandblasting tubes. They should be properly sized and fitted securely. Abrasion-resistant hoses are also designed to be easy to clean.
Hoses can be connected to different couplings including abrasion resistant hose fittings or quick disconnects. They can be connected to other equipment such as compressed air, guns, and nozzles.
Sandblast hoses have a handle installed at the nozzle that connects pneumatically to the inlet and outlet valves on the blast machine. By depressing the handle, the operator activates the nozzle and starts blasting; releasing the handle deactivates the nozzle and stops the process. This is an effective way to prevent accidental activation of the nozzle, which can cause injuries and damage to the work area. The handle opens a safety petcock at the inlet valve, which closes when the operator releases it. This stops the flow of fluid into the hose.
production standards for wear-resistant blasting hose
It's vital to choose a blast hose that is made with quality materials and has a long lifespan. This will reduce the need for frequent repairs and replacements, which can increase productivity. In addition, a high-quality hose is also less likely to break under the intense pressure of sandblasting, which can lead to accidents and injuries.
The material used in the manufacture of a blast hose determines how much wear it can withstand. Cheaper hoses are made with lower-grade materials and can wear out in just a few hours. Comparatively, sandblasting hoses of higher quality can last between 400 and 500 hours.
Blast hoses form an integral part of the blast system. They carry air and abrasive between the blast pot and the nozzle. It is therefore essential that the material used to make them can withstand both the pressure and the velocity of the abrasive that will be blasted.
It's also important to ensure that the blast hose is properly sized. A blast hose that is too small will result in air pressure losses, which can have a significant impact on efficiency and productivity. A good rule of thumb is to make sure that the hose is 3 times bigger than the nozzle size. This will ensure that the abrasive is adequately dispersed and not lost.