It is important to know the specifications and characteristics of fiber-braided hoses in order to choose the right hose for your needs. In addition to abrasion resistance and corrosion protection, hoses must also withstand varying temperature ranges and working pressure.
Hoses that use a textile or steel wire braid are more flexible than spiral hoses. This is because the wires/textile fibers in the layer are parallel to each other and do not cross over one another.
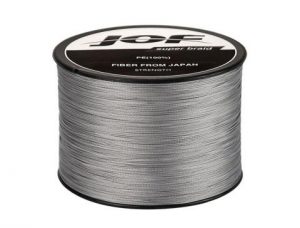
How fiber braided hose can extend service life
The right hose product is critical to extending a hydraulic system's life. Thermoplastic hoses can easily handle high temperatures and environmental stress that would break down rubber products and cause premature hose failure, safety risks and costly downtime. These hoses offer many additional benefits over their rubber counterparts, including higher abrasion resistant, consistent lengths and fewer leaking points.
The reinforcement layer is the muscle of all hydraulic hoses and determines the working pressure of the hose. It can be made from fiber, stainless steel or another material. The type of reinforcement directly affects the end-use performance of the hose.
There are two common styles of hydraulic hose reinforcement: braided and spiral wrap. A braided hose consists of multiple layers of textile fibers or wire that are twisted. The wires or fibers are arranged in layers at a specific angle to create a stronger hose. This hose can support a certain working pressure. A braided hose can also be more flexible than spiral-wound hoses, with a smaller minimum bend radius.
A helix-wrap hose is made of helical coils that are monofilament. This adds strength to the hose and prevents it from collapsing when under vacuum pressure. A helix-wrapped hose can have a lower rating of pressure than a braided one, and has better resistance to impulse loads than a plain braided one because the helixes don't overlap and rub against each other.
the reason for the fracture of the inner steel wire layer of the fiber braided hose
The hose is more likely to break at the bend when a fluid system experiences an abrupt pressure spike. This can lead to dangerous fluids being ejected quickly, which could harm equipment and personnel. Selecting the right hose for the application is essential to preventing this. Braided hoses are ideal for low to medium, less intensive pressure applications and spiral hoses are best for high-pressure and frequent pressure surges.
While wire reinforcement offers the hose great tensile strength, it has little bending or compression strength. It is also highly susceptible to corrosion. To combat this, the hose's inner tube is coated with an anti-corrosion material. The coating can extend the hose's service life significantly.
Optical microscopy of a ruptured hose shows that the first and second reinforcing layers have been chemically degraded to ammonium salts of terephthalic acid (ammonolysis). Moreover, optical fractography indicates that the hose rupture originated on the inside surface of the inner tube layer. The rupture then spread to the outside surface, and longitudinally along hose. Fractographic features confirmed that there were no foreign particles at the fracture site. Higher-magnification views of the fracture surfaces are shown in Figs. 4a-d. The fracture surface nearest the rupture origin has a mist hackle and a branching crack into the inner tube.
the main raw materials used in fiber braided hose
The choice of raw materials is crucial to the performance of a hose. A hose's reinforcement is its "muscle." Braids come in various wire thickness and pitch angle, which impact flexibility, strength (pressure rating), and temperature performance. The right braids, paired with the right core and cover materials, can ensure that a hose performs to the highest standards in critical fluid systems.
The cost and quality of a hose will also be affected by the raw materials used. Stainless steel braids, for example, are often more expensive than nylon or polyurethane. However, they will last longer and provide better value in the long run. The key is to find a supplier that is willing to collaborate with you on hose design.
The right raw materials can help to ensure that your industrial rubber hose is made according to your specifications and ready for immediate application. This will help you avoid costly production delays, and get the most from your hose. For example, a higher-quality reinforcement can allow your hose to be used for high pressure applications where the minimum radius of bend is a major concern. A hose with stainless-steel reinforcement can have a smaller minimum bend radius than spiral hoses that have the same pressure rating.