Rubber hoses can be used in many industries. There are many things to consider when choosing the right hose, whether you need an air brake or fluid power hose.
Spiral wrapping is a common method for making large rubber hoses. This type of hose is usually made with reinforced and outer layers to withstand high pressures.
characteristics of large diameter rubber hose
Rubber hoses are used to transport fluid in hydraulic or other process systems. It is a flexible conduit with multiple material layers that can withstand the pressure in the system it is placed in.
A rubber hose generally has three layers: a seamless synthetic rubber tub; one or more reinforcing layers made of braided, spiraled, or synthetic fiber, and an outer cover. Each layer is a unique design feature determined by the fluid, temperature and pressure ranges it is intended for.
The motor vehicle industry is the largest consumer of hoses, accounting for over one-third of total hose demand. This includes OEM and replacement hoses that are used in engines, steering and brake systems, as well as other key components.
High-value, customized hoses designed to function in environmentally harsh, under-the-hood applications also support demand. These hoses are typically designed for increased abrasion resistance and consistent long lengths to reduce leak points.
Another common material is thermoplastic, which offers a wide variety of added value over rubber counterparts. Thermoplastic hose can be thermoformed into custom shapes to meet customer application requirements. This allows for easier routing and less scrap. Additionally, thermoplastic hose is typically 20% smaller than comparable rubber hose in outer diameter, making it ideal for use on equipment where space is limited.
the method of prolonging the service life of large diameter rubber hose
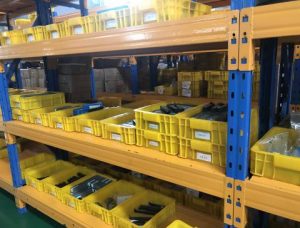
During production, hose material is subjected to a number of tests. These tests include abrasion testing, absorption testing and accelerated life testing.
These tests determine the extent to which the hose deteriorates under service conditions. They also help the hose manufacturer design and develop better products.
These test results can also be used to determine the best hose materials for each application. It is important to ensure that the hose material you choose is compatible with the fluid being conveyed. This includes temperature and concentration.
Hoses that aren't compatible with the fluid being conveyed will reduce their service life. Hose manufacturers offer material compatibility charts to help avoid this.
Some hoses have special designs for improved flexibility. These include convoluted hoses, which incorporate layers of tape to form helical ridges and grooves.
Vulcanization is another method to increase the flexibility of a Hose. This chemical process extends the elastic properties rubber compounds over a wide temperature range.
Large diameter hose should not be stored in direct sunlight and in a controlled area. Bulk rubber hose has a shelf-life of 40 quarters (10 year) from the date it was manufactured, while thermoplastic hose has an unrestricted shelf life.
large-diameter rubber hose steel wire layer fault
The steel wire layer fault is an important cause of hose failure. During the production process, it is necessary to select the correct core and outer casing, and control the amount of buckling and system pressure in the assembly. The correct size and amount of buckling can effectively weaken the bending and twisting stress of the rubber hose and make the hose more durable.
There are many factors that can impact the service life of large-diameter rubber hoses. For example, hoses that are routed around tight corners incorrectly can cause extra stress on the hose during operation. This can lead to leaking crimps and bursts along the stress point of the bend.
External damage to the hose cover or carcass is another reason for hose failure. Kinks, crushed sections and cover damage will eventually expose the reinforcing steel wire to abrasion and break down the reinforcing steel wire.
A large-diameter rubberhose should have at minimum three types of joint cores or outer caps: (1) Antipull-out structure, (2) Rectangular structure, (3) Inner locking structure. Compared with the anti-pull-out structure joint core, the rectangular structure joint core has a higher strength. This joint core is suitable to use with resin hose, steel wire wound and other types hoses.